FULFILLMENT
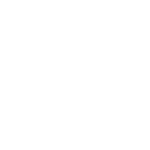
3-POINT VERIFICATION
Drive’s scan verification capabilities ensure that every shipment is accurately picked, packed, and shipped in the most timely and cost-effective manner.
3-Point verification is powered by DriveLine – a comprehensive warehouse management software that streamlines the fulfillment process while giving you peace of mind, visibility, and security that comes with real-time tracking through the entirety of the picking, packing, and shipping process.
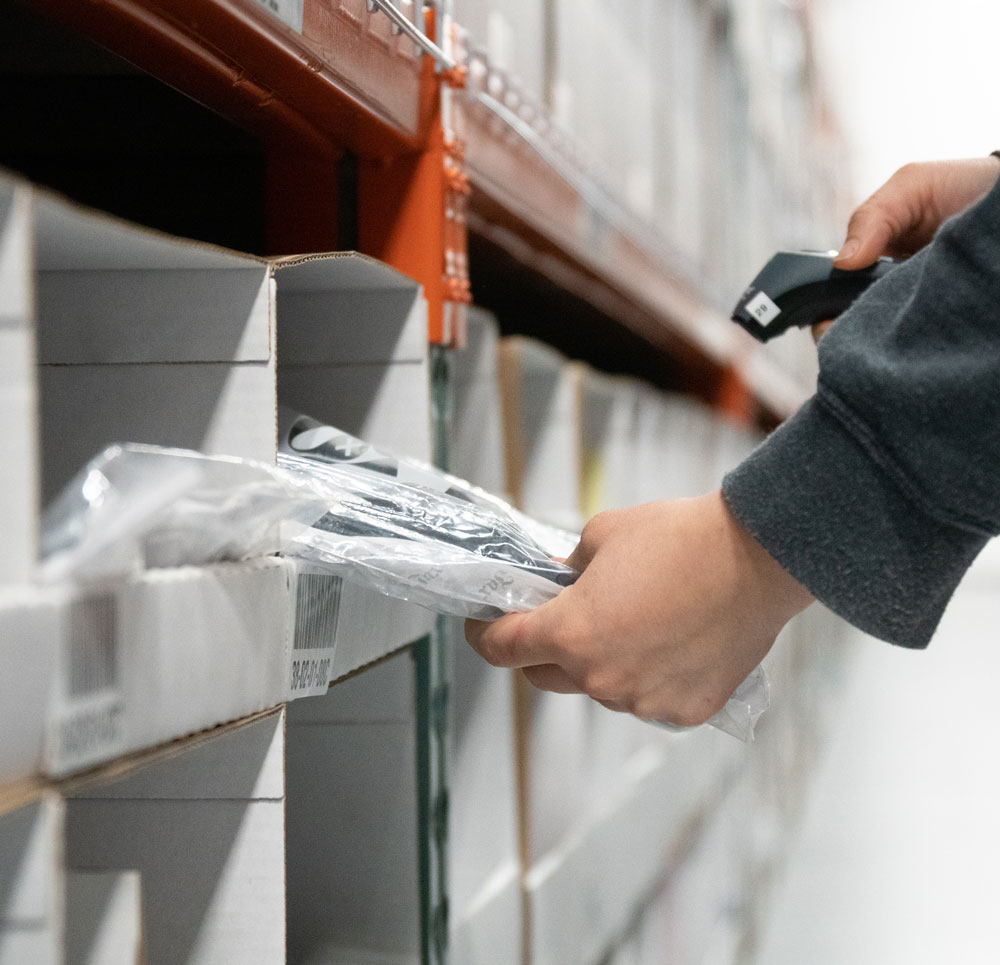
PICK.
The first stage in the order fulfillment process is picking. Once a warehouse picking team is assigned, the picker receives a packing list of items, the exact quantities, and locations in our facility, collecting the items from their respective positions. Correct items are then scanned and verified in preparation for packing.
PACK.
Once items have been picked, a team will begin meticulously packing each shipment. At Drive, we value the ability to design and create custom packaging and kits that align with your branding preferences because no two customers are the same, and neither are their shipping solutions. No matter the task, we believe in making the first impression on a customer, a memorable one. From the most durable and cost-effective packages to appealing shipping materials, we’ve got you covered.
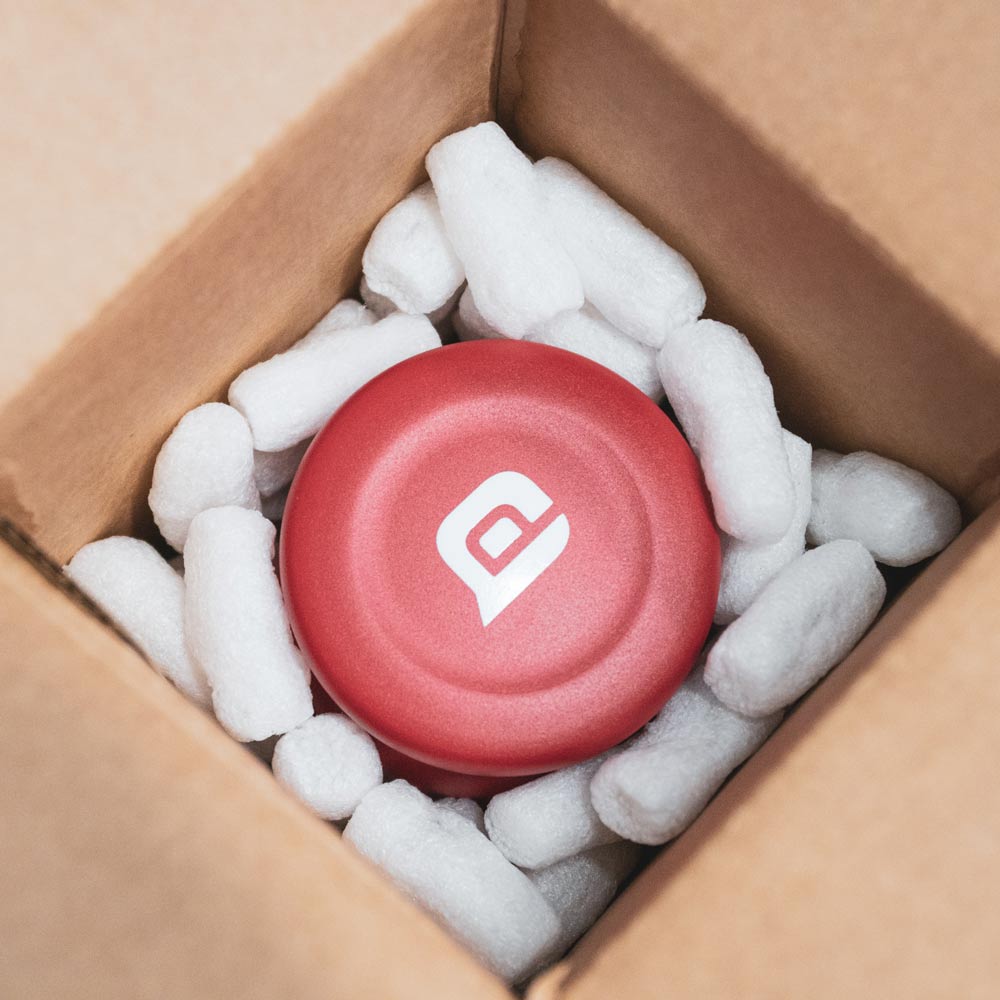
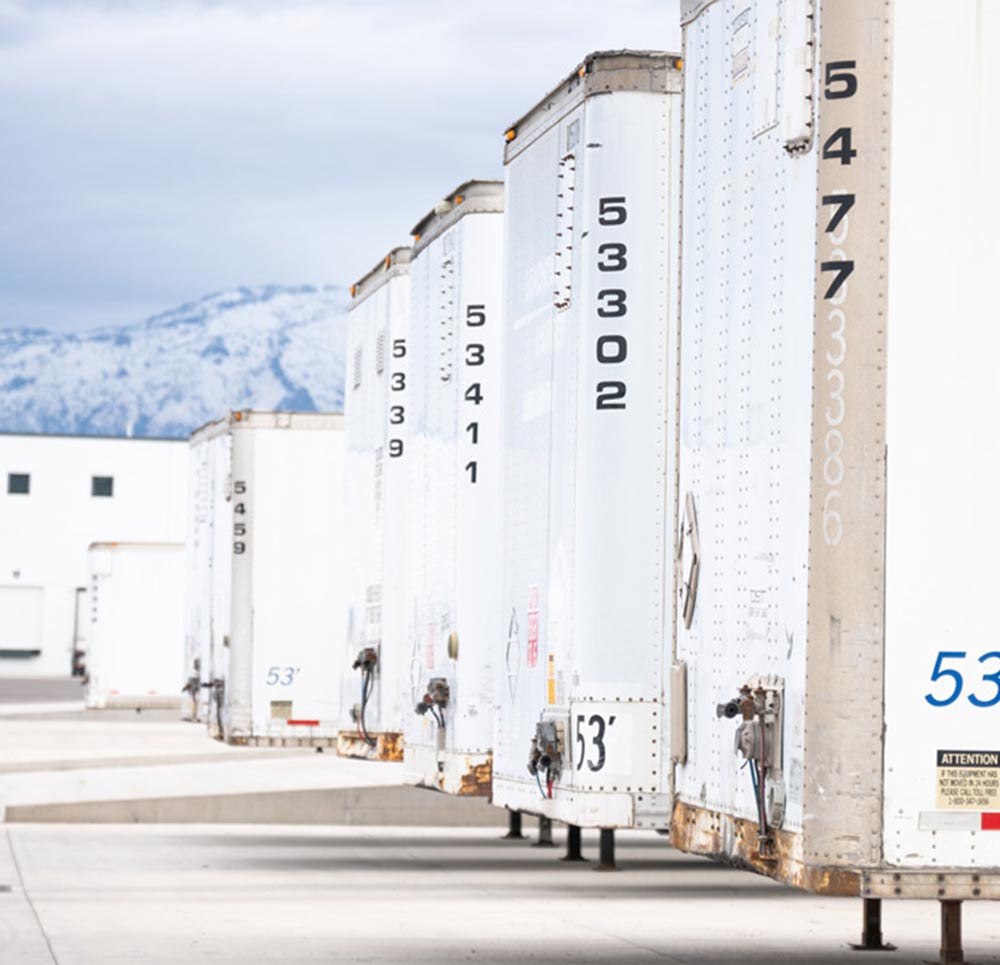
SHIP.
The last stage of the process involves the shipping of ordered items. Packaged orders are then labeled and verified before being recieved by a third-party courier service. Whatever shipping method a customer selects automatically integrates into the tracking details. Then, a confirmation email is sent directly to the end customer and shop merchant.
PICK. PACK. SHIP
Explore how automated high capacity fulfillment and precise Pick Pack Ship Fulfillment transparency can streamline your supply chain logistics and bottom line today.