eCommerce selling and fulfillment require a clear understanding of user needs and how to best cater to them through your brand and product messaging strategies. Minor adjustments like the placement and style of packaging materials can make or break the unboxing experience.
While catering to an onslaught of customer needs can be an extensive and time-consuming process, Kitting and Assembly fulfillment saves you time and money by pairing and packaging product components or items for shipment in the most organized and efficient way possible. This ensures that products and the proper components are grouped and packed together, quickly delivered in the expected and desired fashion.
How does the process work?
The kitting and assembly process is a warehouse inventory management task performed after merchandise is delivered from the manufacturer. Depending on how the manufacturer ships the merchandise, our teams work package products in bulk the way you need. Whether for a special promotion or single offering, the point of creating kits is to have a ready-to-ship kit finished once a customer places an order. Unlike a regular order where you can’t predict what a customer will order together, kitting is when a predetermined combination of products, promoted and sold together, which expedites the retail fulfillment process.
Why use kitting and assembly?
While kitting and assembly help maximize sales and efficiency, it’s important to note that it’s not always necessary. Consulting with a 3PL logistics partner like Drive Fulfillment can help you make sense of your needs and whether your business can profit from the process.
What is the difference between kitting and bundling?
The primary difference between kitting and bundling is that kitting requires fulfillment teams to assemble multiple component pieces that are separate at inventory into one specific order. A bundle contains several items or products (not one with multiple pieces) sold and shipped together. Bundles don’t require the unique assembly of individual components to ship an order, like kitting. Bundling groups multiple and distinct items under one main SKU. A bundle SKU is not a single product on its own, but rather a packet that includes two or more items.
How do we take it a step further?
At Drive Fulfillment, our client engagement specialists work with meticulous care to ensure your items are assembled according to precise specifications. With years of proven experience, innovative technology, and automation capabilities, we make it easy to stay ahead of your competitors.
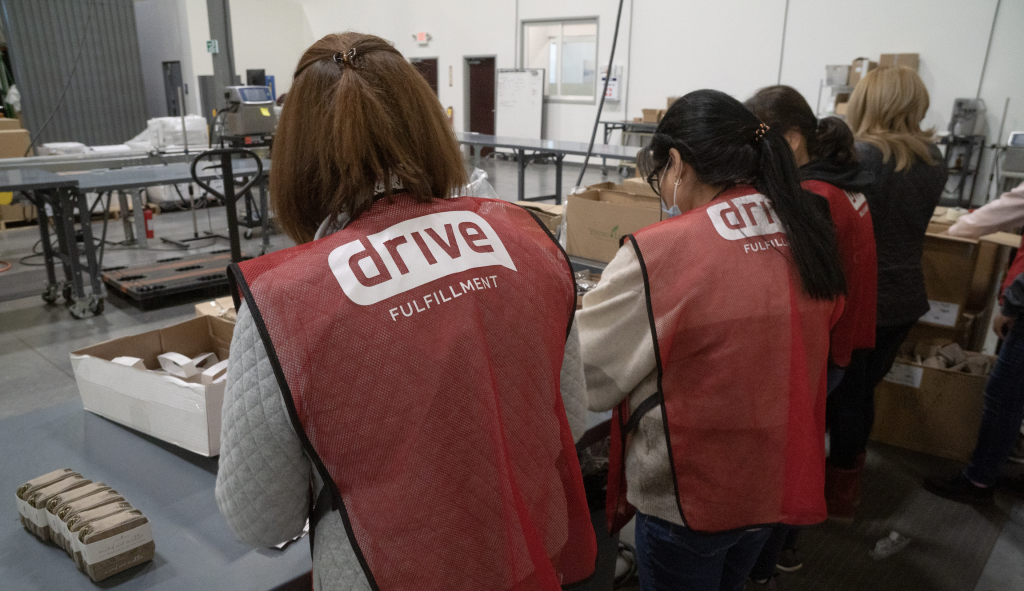
We work with each customer to ensure their items are assembled exactly as intended before orders are shipped to customers. This process reduces shipping costs and helps scale your business as quickly and efficiently as possible. It’s never been easier to bundle products, request kitting, and manage multiple SKUs and products simultaneously.
Common kitting and assembly needs include:
When multiple component pieces arrive separately and need to be assembled in one shipment.
When you require inventory prepared in a particular way for customers.
When you require the breaking down of inventory from a case into single units.
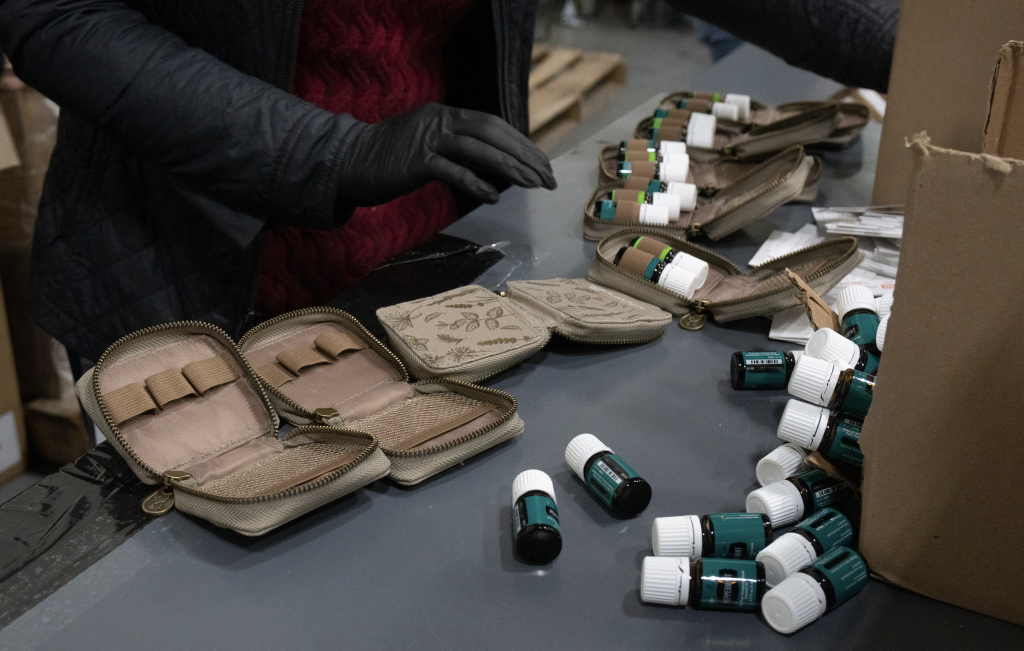
Taking a step further than assembling and bundling components, we employ a variety of innovative highspeed packaging machines, like shrink wrapping and custom packaging, that polish the process and ensure your products are safe and protected on top of being correctly assembled.
Shrinkwrapping:
Shrinkwrap is a highly effective method to package and protect your merchandise from variables like environmental damage, contaminants, and humidity. Shrinkwrapping prolongs the life of products that would otherwise spoil, efficiently saving you time and money by replacing damaged items.
Our Hy-speed shrinkwrapping and sleeving capabilities powered by Shanklin utilize enhanced servo motor controls, robust mechanical design, and intuitive picture-based controls and navigation to accommodate evolving production requirements. These fast shrink systems can process up to 180 packages per minute of varying sizes with fully automatic product handling making for the most efficient, high-quality, and smooth processing on the market.
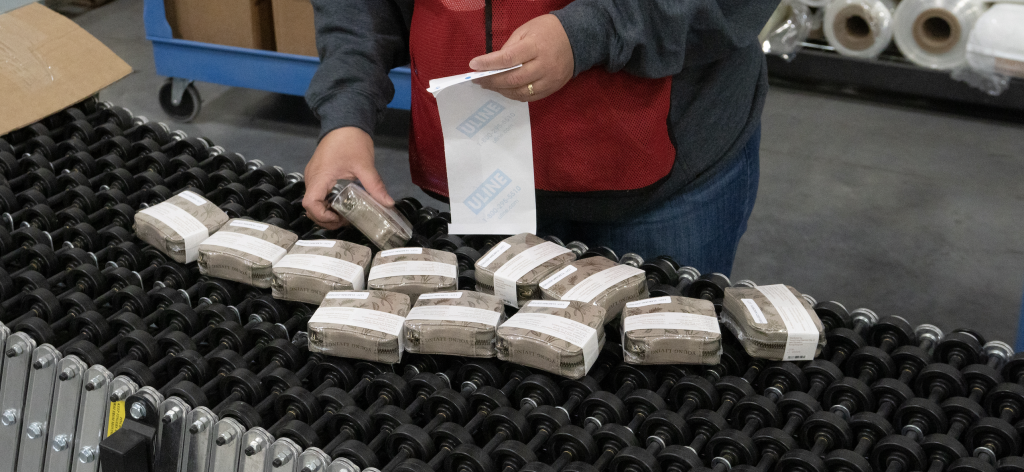
Features & Benefits:
Fast and dependable high-speed machine with fully automatic continuous flow operation.
Versatile and runs well at high and low speeds, capable of handling a wide range of packages.
Automatically compensates for package length changes.
An automatic film advance system allows light and flexible products to be wrapped with ease.
Picture-based HMI touchscreen offers easy navigation for the system operator.